CEE Students Compete in ASCE New England Regional Steel Bridge Competition
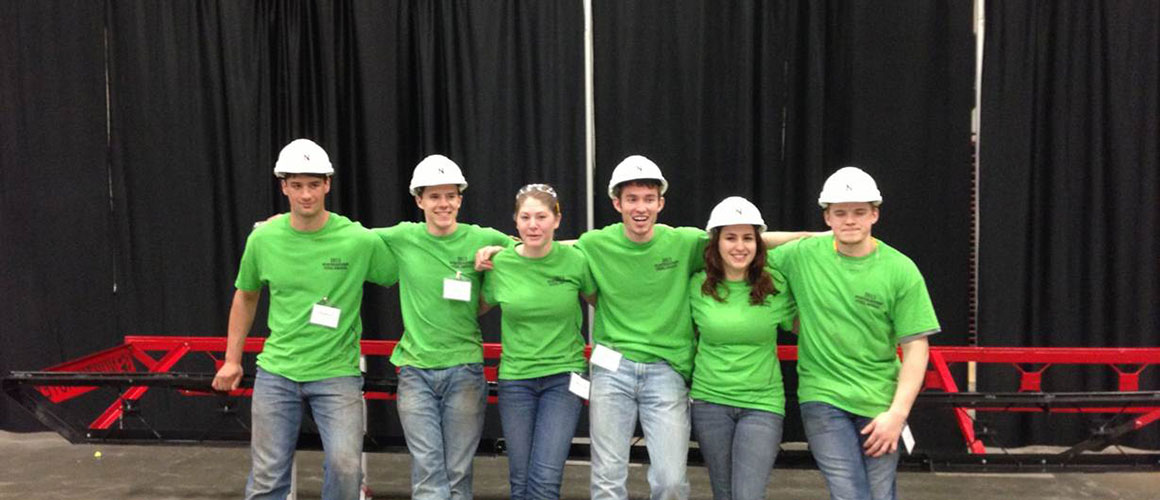
The NU Steel Bridge team recently participated in the ASCE New England Regional Steel Bridge Competition hosted by MIT on April 20th. The Student Steel Bridge Competition is intended to enhance civil engineering students’ education by challenging them to conceptualize, design, erect, and test a steel structure that maximizes performance and economy. The NU Steel Bridge team was led by seniors who guided a group of underclassmen who designed and built the bridge. The NU bridge was successfully constructed and load tested at the competition. Congratulations to the NU Steel Bridge team for their accomplishments!
Source: News @ Northeastern
For many civil engineers, the annual steel bridge competition might as well be the Super Bowl. It’s a big deal — university teams all over the country spend many months, and many late nights, coming up with a bridge design, fabricating the pieces, and building their own personal masterpiece. The bridges are serious, too: they need to be able to hold 2500 pounds of steel! That’s how much a Kia Rio weighs, just in case you were wondering.
Northeastern used to have its own team, but with seniors pursuing their capstone projects strapped for time and younger students still learning the basics of engineering, it fizzled out after just a few years. A true steel bridge diehard, Civil and Environmental Engineering department chair Jerry Hajjar took matters into his own hands.…or rather, he placed matters in the hands of Matt Pellegrino, a civil engineering student soon to graduate with a BS/MS in structural engineering.
Pellegrino did for the Northeastern Steel Bridge Team what Walter Matthau did for the Bad News Bears.…only instead of starting with a bunch of terrible players, he had, well, no players. He recruited 25 students evenly dispersed across years, and got to work.
While most steel bridge teams have a single goal–to build an awesome bridge that wins the competition–Pellegrino had another challenge. He also had to build his team to be sustainable, so that it would last long after he’d left campus (incidentally, for a bridge engineering job in Dallas, which he’ll be starting just a few weeks after tossing his cap in the air this Friday).

How does one build a sustainable team? With nearly two decades of leadership training with the Boyscouts of America, Pellegrino had something of an idea: You have to make each member of the team an integral part of the project, he told me. Instead of designing an elaborate suspension bridge that requires computational analysis to determine the multiple forces on the structure, the team chose a simpler truss bridge design. “It’s like the Tobin rather than the Zakim,” Pellegrino explained.
With the simpler structure, the younger students could understand the system they were working with, they actually got to be a part of it. “Then, because they were involved in the design, they’re more inclined to stay around and build the bridge and see it come up,” said Pellegrino.
They started designing last fall, then around Christmas time put in an order for steel. Northeastern alumnus Todd Stevens of Dimension Fabrications in Albany, NY donated all of it. “That guy was like Santa Claus,” said Pellegrino.
With a few hundred pounds of steel in hand, they spent many, many hours between January and mid-April in the Snell Engineering building. They machined all of the pieces, creating their own giant Kinex set, and then assembled them into their mini-Tobin. A few days before the Northeastern Regional Competition, they carefully broke it down into a few sections. Just like the shrunken bridge, the sections had to fit real world specifications. They had to be smaller than a 3’x4“x5” box (a scaled version of a tractor trailer bed), and they had to weigh less than 20 pounds (the scaled weight limits for most roads).
They transported their mini-bridge pieces across the river to MIT where 10 teams competed for a spot in the national competition. Five of Pellegrino’s teammates assembled the bridge on the clock and then bit their fingernails as they placed 100 25-pound pieces of cut steel across the top: The bridge stood the test of steel!
They also managed to overcome the Achilles heel that had plagued the old Northeastern Steel Bridge Team: when pulled from a certain point, the bridge moved less than a half inch in the lateral direction (as you might imagine, shaky bridges aren’t much fun in real life).
While they didn’t come in first place…or really anywhere close to first place, the team feels incredibly successful in its mission. They built their team, and their bridge, to be sustainable against the expected forces. Instead of 2500 pounds of steel, the student group has to withstand the constant flux of students coming and going. They’ll need to work together to pass their skill sets from one generation to the next.
Pellegrino said the effort was in no way a one-man show. Every member of the team had a role to play, and he is confident that after he’s been in Dallas for many years designing life-size bridges, the Northeastern Steel Bridge Team will still be building their mini ones.